Cobots and The Future of Manufacturing: A Quick Glimpse!
The COVID-19 pandemic has accentuated the need for resilient supply chains and human-machine collaboration at work. Full or partial shutdowns, as well as social distancing regulations, impose factories and workspaces to operate with the minimal onsite crew. Despite labor shortages, supply chain disruptions, and other production challenges, manufacturers are under constant pressure to respond to the evolving market needs. The demands for mass customization, quality expectations, faster product cycles, and product variability are at an all-time high. Tackling these persistent challenges requires combining human skill and ingenuity with the strength and speed of robots. To bring the best of both worlds – human creativity and robotic precision – manufacturers should adopt cobots (collaborative robots) that can reduce human interaction in feasible situations and accelerate production cycles.
Cobots allow manufacturers to maximize production and address the changing demands while ensuring the safety of their employees, clients, and partners. Why are cobots the future of manufacturing? How do they help build manufacturing resilience? Let’s explore further in this blog.
Read more: What are cobots and how can they benefit industries
Cobots Enhance Manufacturing Efficiency
Collaborative robots or cobots are designed to safely work alongside humans in tedious, dull, and hazardous environments. Unlike the traditional industrial robots that work in fenced premises to avoid close proximity with people, cobots operate in a shared workspace alongside human labor. For instance, a robot that helps humans sort foam chips in a lab is a cobot, while a robot welding a sharp cutting tool in a restricted factory area is a typical industrial robot.
Conventional industrial robots have long enabled manufacturers to leverage automation and compensate for labor shortages, but they are typically designed to execute one specific task. Moreover, they lack the cognitive capabilities possessed by humans to reprogram their operations based on new circumstances. In contrast, cobots don’t require heavy, pre-programmed actuators to drive them. Cobot motions are steered by computer-controlled manipulators, such as robotic arms, which are supervised by humans. Thus, cobots facilitate effective human-machine collaboration at work.
Cobots can be programmed to perform a wide range of tasks in a factory setting such as handling materials, assembling items, palletizing, packaging, and labeling, inspecting product quality, welding, press-fitting, driving screws and nuts, and tending machines. While cobots attend these mind-numbing jobs, human workers can focus on tasks that require immense resourcefulness and reasoning.
Read more: Digital Transformation in Manufacturing
Benefits of Cobots in Manufacturing
Modern manufacturing requires effective human-machine collaboration to cut expenses, reduce time-to-market, and address growing customer demands. Here’s how cobots empower manufacturing enterprises.
1. Easy to Deploy and Program
It takes days and weeks to install and program a traditional industrial robot. A cobot, on the other hand, can be set up in less than an hour. They are lighter than conventional robots. With user-friendly mobile applications and customized software, you can swiftly program the cobot to get started. Right software configurations enable cobots to learn new actions, without any specialized training. Using intuitive 3D visualizations or simple graphical representations, you can move the robot arm to preferred waypoints. Your employees can focus on more critical tasks while the cobot takes care of mundane jobs.
2. Flexible to Perform Different Tasks
Cobots can be easily shifted from one workstation to another due to their flexible hardware. With minimal software customizations, cobots can be re-deployed or repurposed to perform different functions across various departments. For example, a cobot that performs picking and packing can be re-programmed as a filler by replacing its robotic arm with a tube and nozzle.
Read more: Challenges, Opportunities, and Technologies That Will Revolutionize Manufacturing
3. Save Production Cost and Time
A study conducted by the World Economic Forum in association with Advanced Robotics for Manufacturing found that collaborative robots can cut nearly two-thirds of the cycle time required to pack boxes onto pallets. Because cobots are designed to work without any breaks, they reduce the idle time between cycles. The International Society of Automation reports that cobots can save production costs by reducing 75% of manual labor. Traditional robots increase the installation costs for manufacturers as they need to set up additional safety measures around the deployment area. Cobots don’t incur such extra expenses as they can be set up in close proximity to humans.
4. Improve Employee Engagement and Productivity
Cobots work in collaboration with people to refine and process the tasks better. They can never replace the human touch in production. When cobots take care of repetitive tasks such as screwing a bottle or packing medical equipment, employees can focus on more important functions such as running quality checks or inspecting a worksite. It allows manufacturers to optimize their productivity and boost employee morale. Businesses can also prepare their workforces to learn new skills.
5. Maintain Consistency and Accuracy
From the first to the hundredth task, cobots maintain the same level of accuracy and consistency. Humans can get drained easily, whereas a cobot never deviates from the actions for which it is set up. This helps ensure high product quality and uniformity. With the right software and hardware configurations, cobots can produce more finished goods at an incredible pace, faster than handcrafting.
Cobots and The Future of Manufacturing
Industry 4.0 paved the way for automation and smart manufacturing powered by data-driven technologies such as IoT, cyber-physical systems, wearables, AR, cloud computing, artificial intelligence, cognitive computing, and so on. Though the sole focus of Industry 4.0 is to improve process efficiency through physical and digital integration, it accidentally ignores the significance of human value in process optimization. Industry 5.0 re-shifts its focus on human value by fusing the roles of mechanical components and human workers in production. This makes cobots the very foundation of the next wave of the industrial revolution, that is, Industry 5.0.
Denmark-based Universal Robots reports that cobots are at the heart of Industry 5.0. Cobots democratize robotic capabilities, thereby serving as a personal tool that can be leveraged by any member of the workforce to apply creative skills and generate more value. Cobots can be used as a plug-and-play solution across a variety of manufacturing and industrial operations such as automotive production, food processing, chemical plants, medical devices, and kits, among others.
Since they collaborate well with humans in a safe environment, cobots will:
- augment intelligent decision-making,
- drive high-quality products to the market,
- enable mass customization and personalization,
- optimize manufacturing costs,
- generate new job roles (eg: Chief Robotics Officer), and
- boost virtual education to make the most of collaborative robotics.
Read more: How Custom Software Development Helps Manufacturing Industry
How We Help Manufacturers Leverage Cobots and Other Emerging Technologies
As technology matures, manufacturing enterprises need to build use cases that prove the inevitability of human-robot collaboration. We help develop POCs and use cases that demonstrate how your business can benefit from cobots. Our experts can develop your cobot management software or mobile app from scratch or customize your existing software to address the evolving market demands. Fingent can work along with your cobot hardware manufacturers to develop a robust software orchestration layer that can control the movement of your cobots. We also simplify the training process to help you get started in no time.
Stay up to date on what's new
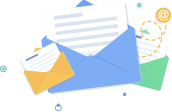
Recommended Posts
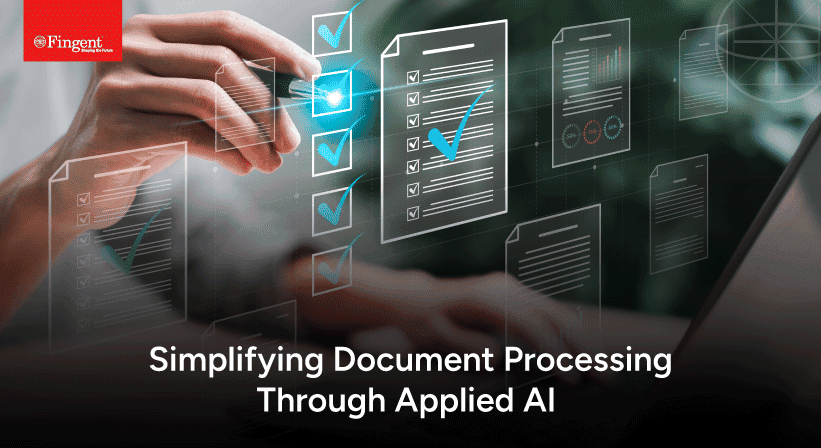
18 Apr 2024 B2B
Applied AI For Document Processing
"It's becoming increasingly clear that AI is the future, and almost everything else is a sideshow." - World-renowned computer scientist Geoff Hinton AI has taken over almost every aspect of……
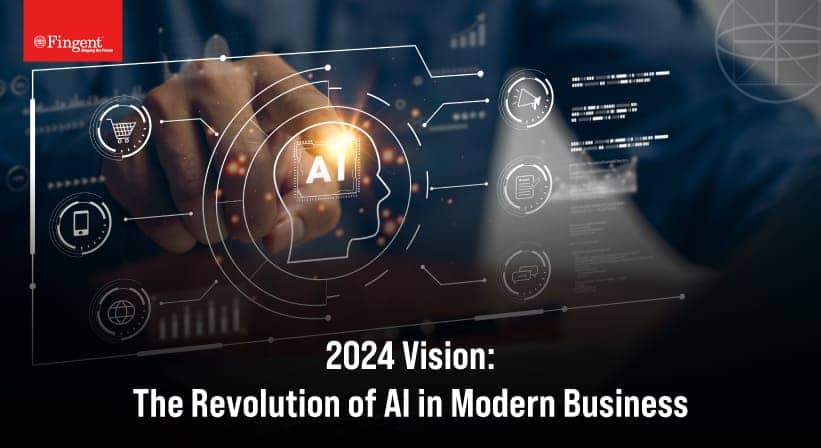
10 Jan 2024 B2B
AI Trends Set to Transform Businesses in 2024
In the dynamic realm of modern business, the profound impact of artificial intelligence (AI) continues to unfold, reshaping industries and redefining conventional practices. As we step into 2024, the transformative……
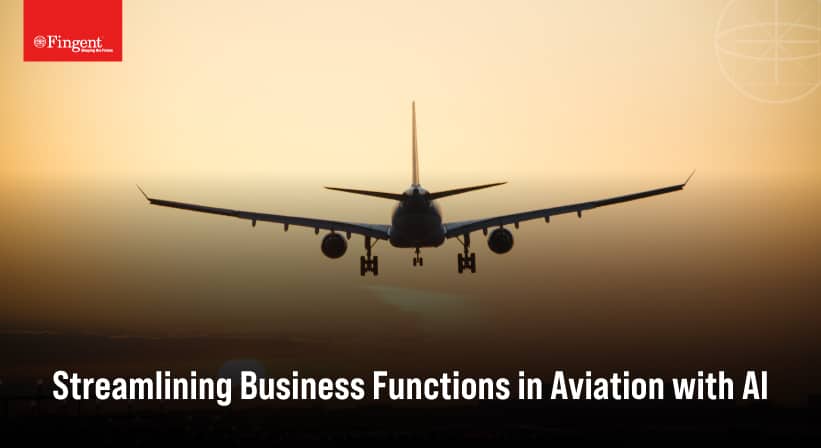
26 Nov 2023 B2B
Finding Success in the Aviation Business with AI
“Aviation is the branch of engineering that is least forgiving of mistakes.” - Freeman Dyson, British-American theoretical physicist and mathematician. The truth in that statement is sobering indeed. The precision……
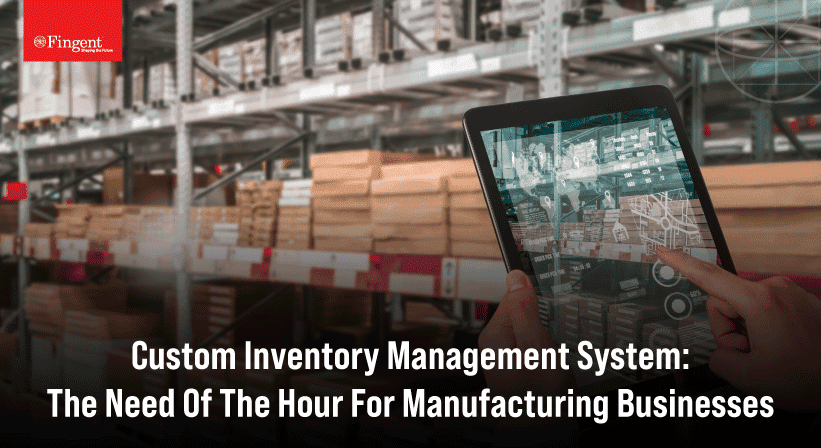
22 Nov 2023 B2B
Custom Inventory Management System: The Need Of The Hour For Manufacturing Businesses
In the competitive manufacturing world, being average won't secure a win. Businesses need technology to outperform competitors, reduce costs, and build a stellar reputation that echoes through the manufacturing jungle.……
Featured Blogs
Stay up to date on
what's new
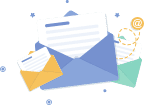
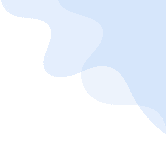
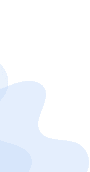